|
Post by carlyd on Jul 9, 2015 20:55:34 GMT
I had to buy 2 new bottom ball joints as they were split when I removed them, strange as the car has never been driven yet. I also had huge problems removing the bottom ball joints as the shaft just spun around when I turned the nut. I decided to cut a slot in the top so I could hold it with a screw driver, it wouldn't be a bad idea for the manufacturers to do this as standard.  I have read the front upright build guide and still managed to get the hubs the wrong way around. So for anyone else do this job, the two holes go to the bottom as the picture below. 
|
|
|
Post by mawdo81 on Jul 9, 2015 20:56:03 GMT
You can get a bolt extractor (eBay or halfords) that will drill into the remainder of the bolt with a left hand thread, as it tightens it loosens the damaged bolt...but for that to work you'll need to hold the other half still and that might be an issue.
What was the grade of bolt that snapped?
|
|
|
Post by airforceone on Jul 9, 2015 21:29:22 GMT
You need something called an easy-out. You basically drill a hole in the remaining part of the bolt then this easy-out screws into the hole and allows you to screw it out. Your local garage should be able to help you out for a few quid.
I used high tensile bolts (M12, 10.9) on mine as the rally design ones aren't long enough to screw through the fender bracket and into the spindle.
Rally design also sell the rubber boots for the bottom ball joints, at £4.50 a pair it's cheaper than buying 2 brand new joints.
The track rod ends need to be compressed into the bracket, this stops the inner shaft from turning a basic c clamp or even some mole grips should be good enough to do the job. As the shaft is tapered forcing the arm down on the thicker part of the shaft holds it in place and should stop it from spinning.
|
|
|
Post by kiwicanfly on Jul 10, 2015 8:19:38 GMT
It looks like a case of too much locktite, you should only need a little and even then, depending on type, you may need to warm the axle to soften it.
You have twisted the head off, it is not really a fault of too weak a bolt, more the load type applied trying to combat the locktite.
I would doubt an easy-out would remove it now and you may then be faced with a broken easy-out stuck in there as well.
I would contact RD for replacement shafts first, I doubt they will help but worth a try.
Next I would find a friendly engineering company and get them to spin it in a lathe for you, anything but a lathe chuck is likely to damage the bearing diameters if gripped tight enough to be able to force that bolt out.
When replacing I would use a Nordlock washer under the head, you won't need locktite then.
|
|
|
Post by carlyd on Jul 10, 2015 15:35:32 GMT
Yes that locktight is a nightmare once it's set. I just called Rally Design, £16 for a new stub axle so I ordered one 
|
|
|
Post by airforceone on Jul 10, 2015 15:43:31 GMT
Thanks not too bad actually bet the postage was almost as much. When I need something from them I usually get a few other items as the postage tends not to change will a load of small items.
|
|
|
Post by carlyd on Jul 11, 2015 19:14:44 GMT
I'm waiting for the stub axle and ball joints to arrive so I thought I'd tackle the fuel tank. I'm fitting it in the front area where most people fit the radiator. I drilled the drain holes in case of spillage  Then fitted the fuel tank using some spare rubber fuel hose to cushion it against vibrations.   I have the filler in a panel at the front and will box in the fuel filler hose so passengers can't kick it, and to protect the passenger compartment from fuel spillage. 
|
|
|
Post by airforceone on Jul 12, 2015 14:52:52 GMT
Have you checked that the fuel filler hose running across the passenger foot well will pass the IVA you may have to box it in to prevent it being accidently being kicked off.
|
|
|
Post by carlyd on Jul 12, 2015 19:30:06 GMT
Have you checked that the fuel filler hose running across the passenger foot well will pass the IVA you may have to box it in to prevent it being accidently being kicked off. I am gonna box it in anyway. Deano's car passed with this setup so should be ok I'm hoping.
|
|
|
Post by carlyd on Aug 17, 2015 10:46:28 GMT
I have now fitted my bonnet, I decided to go for the pressy quick release catches that a couple of others have used. I had to make a couple of brackets to fit the pressy catches  Then I had to mark the bonnet for the pressy catches.  Then mount the brackets  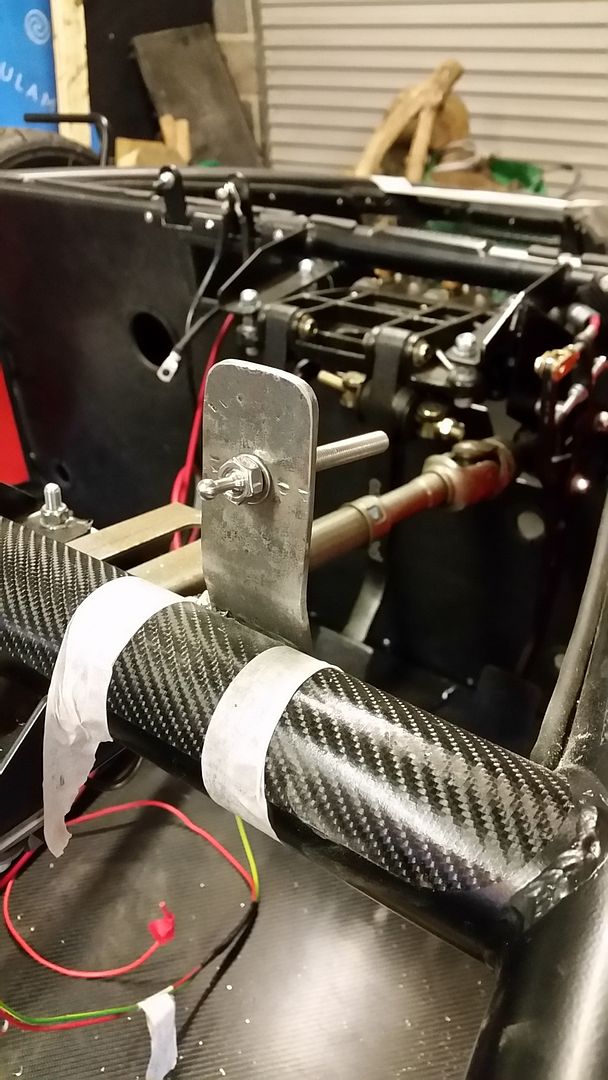 Lots of careful measuring and drilling later - all done.  Then after the pressing catches are finished I fitted the aero catch. Again just lots of measuring and careful drilling required.   
|
|
|
Post by carlyd on Aug 17, 2015 10:53:45 GMT
The handbrake leaver I chose is a mk2 focus one so that the cable pull is central. I cut it down to fit my car as detailed by others but as my tunnel is smaller than most (due to larger seats) I had to make it even smaller than most while still keeping the cable pull central. 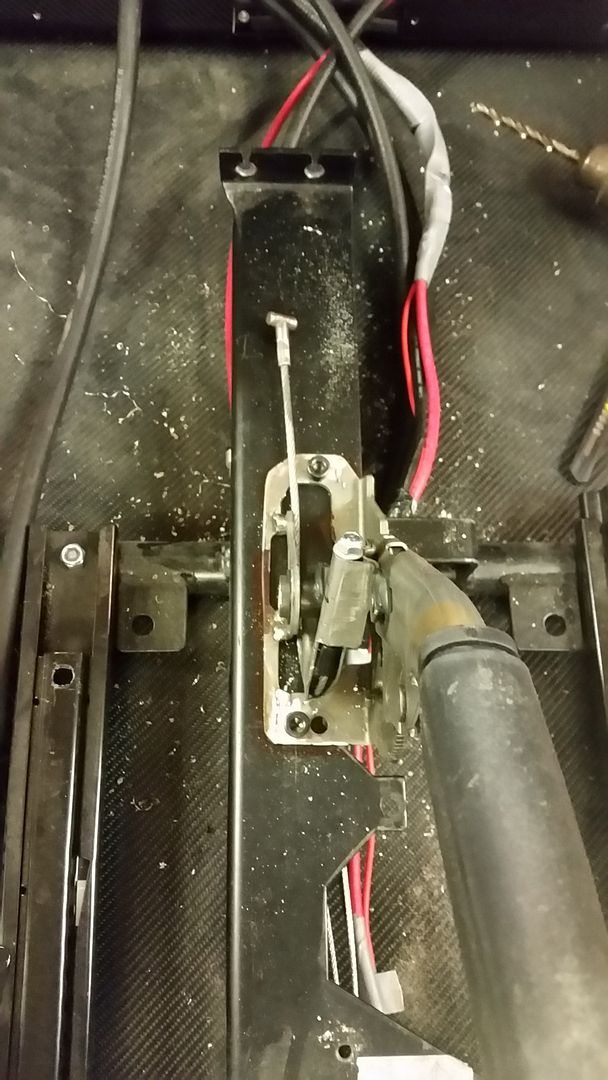  
|
|
|
Post by carlyd on Aug 17, 2015 10:56:41 GMT
I had to have my gear selector cables lengthened, after lots of searching the internet I found www.cable-tec.co.uk/ who lengthened them to over 4 metres for £300. I fitted them and they work perfectly. 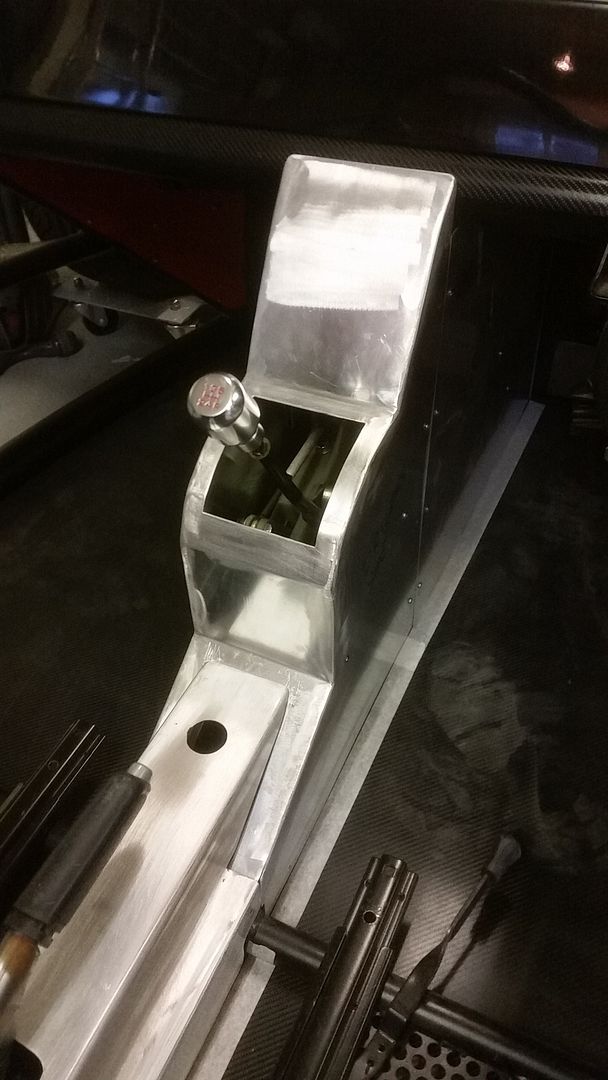 
|
|
|
Post by carlyd on Aug 17, 2015 10:59:43 GMT
I decided to make an aluminium gear selector gate. Paul (Madeye) offered to make one with his CNC machine for me but I thought I'd give it a go at making one by hand. I first make a card template and then cut it out in aluminium.  An hour or so later and lots of filing and polishing and it's done. 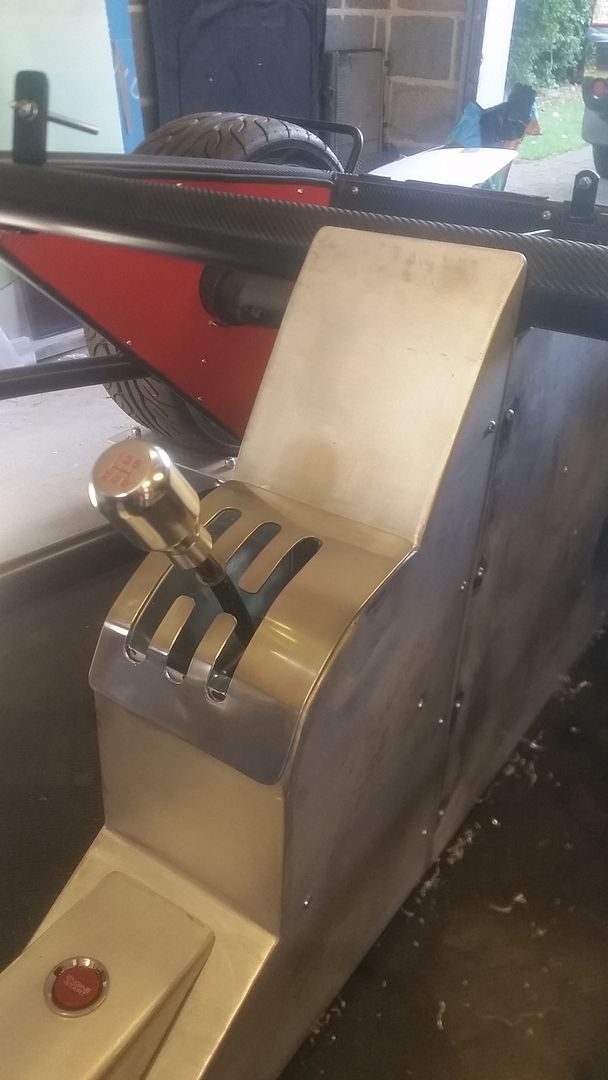 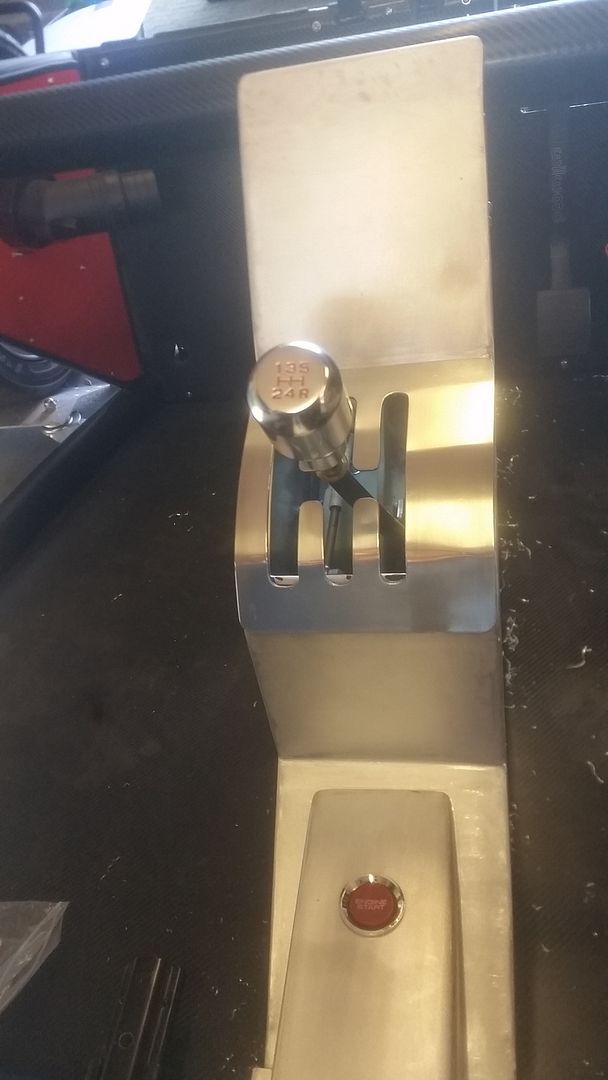 
|
|
|
Post by airforceone on Aug 17, 2015 12:37:12 GMT
That looks nice.
Do you have enough movement of the gear stick to engage the gear fully.
I have the quick shift kit from joker and I have more movement than that.
|
|
|
Post by carlyd on Aug 17, 2015 12:49:22 GMT
That looks nice. Do you have enough movement of the gear stick to engage the gear fully. I have the quick shift kit from joker and I have more movement than that. Yes I made a card template first checking that all gears are fully engaged, and I have tested it after I made the ally version, everything works fine. My setup isn't a ford engine and gearbox though, it's the Honda Type R gearbox and gear selector which given that it's a performance car I would expect the gear throw to be shorter than a standard focus, maybe even shorter than the quick shift. It does feel very solid when putting into gear which gives it a nice quality feel. The material I used is only 2mm though, it could do with being 4 or 5 mm. I may redo this when it's all finished.
|
|