|
Post by carlyd on May 17, 2018 14:48:33 GMT
I wonder if this addition would help. I'm sure it would but you shouldn't need to modify parts like that. But I guess you get what you pay for.
|
|
|
Post by sammy on May 17, 2018 15:41:54 GMT
I do not know if it can help this video. I do not understand anything. But I think I understand that the use of Loctite is recommended.
|
|
|
Post by kiwicanfly on May 17, 2018 16:59:41 GMT
I didn't use a torque wrench but I did have to remove the axle for some reason and managed to sheer the bolt off whilst trying to remove it, so it must have been tight. It's all documented in my build diary. I then switched the bolts for 12.9 allen bolts with threadlock but the passenger side still unsrewed itself. In fact when a potential buyer came to test drive it I noticed the bolt was about 2 - 3 inched out (unscrewed itself) and when I tried to tighten it sheered off again. I had to buy another new one. Very poor design IMHO. Whilst not a witness myself I find it hard to believe an m12 bolt could be unscrewed that far out as this would be more than the thread length on the bolt. Whilst it is obvious that too much torque is a bad thing it is often not appreciated that too little torque can be equally bad if the bolt is subject to cyclic loading such as in this application. This is even worse with the use of high tensile fasteners such as g12.9. www.gatestechzone.com/en/news/2017-11-torque-settingsBasilally if you are not going to torque up a high tensile fastener (greater than g10.9) correctly for whatever reason you are better off using a lower rated (but sufficiently strong) fastener. Whilst this also needs to be torqued correctly is will be succepabtable to failure. Regarding the use of thread locking compound, once used it is impossible to check the tightness of the bolt, for whatever reason, due to the chance of compromising the compound. The joint would need to be stripped cleaned and reassembled.
|
|
|
Post by Stiggy on May 17, 2018 17:47:14 GMT
Rally Design sell them for cars up to 500kg, NOT a GT40.
|
|
|
Post by kiwicanfly on May 17, 2018 18:18:13 GMT
500kg or 5000kg does not negate the need to torque correctly for the selected fastener, the loading simply determines the fastener type and size.
|
|
|
Post by sammy on May 17, 2018 18:48:07 GMT
a possibility would be, for those who can do it, make a stub axle with the same measures as Rally Design, but instead of having an assembly hole, make it with a pin, style Highspec, that is, with an external thread, in order to use a self-locking nut, preferably with m16x1 thread, instead of a bolt as the original.
|
|
|
Post by sammy on May 17, 2018 18:53:24 GMT
Rally Design sell them for cars up to 500kg, NOT a GT40. I'll be wrong, but it seems to me that rally design is for cars up to 950 kg.
|
|
|
Post by Stiggy on May 17, 2018 21:53:05 GMT
500kg or 5000kg does not negate the need to torque correctly for the selected fastener, the loading simply determines the fastener type and size. true, I think they should have put a kiwi in it, sorry i mean to say Keyway!
|
|
|
Post by carlyd on May 18, 2018 13:49:07 GMT
I didn't use a torque wrench but I did have to remove the axle for some reason and managed to sheer the bolt off whilst trying to remove it, so it must have been tight. It's all documented in my build diary. I then switched the bolts for 12.9 allen bolts with threadlock but the passenger side still unsrewed itself. In fact when a potential buyer came to test drive it I noticed the bolt was about 2 - 3 inched out (unscrewed itself) and when I tried to tighten it sheered off again. I had to buy another new one. Very poor design IMHO. Whilst not a witness myself I find it hard to believe an m12 bolt could be unscrewed that far out as this would be more than the thread length on the bolt. I used a longer bolt as my bolt went through the middle of my wingstay too and the standard bolt wasn't long enough. (all shown in my build diary). The whole design of the stub axle and wingstay means that if you don't run the bolt though the wingstay you would have to remove the wingstay if you want to remove the stub axle.
|
|
|
Post by airforceone on May 30, 2018 8:22:48 GMT
Here is a picture from my set up. I switched out the normal nut that came with the hubs for a castle nut and split pin combo. So shouldn't need to worry about loosening off. This mod was carried out ages ago as this issue was mentioned on the forum before. The rear of the stub axle was attached using an M12 bolt with large thick washer with a lock/shake proof washer. 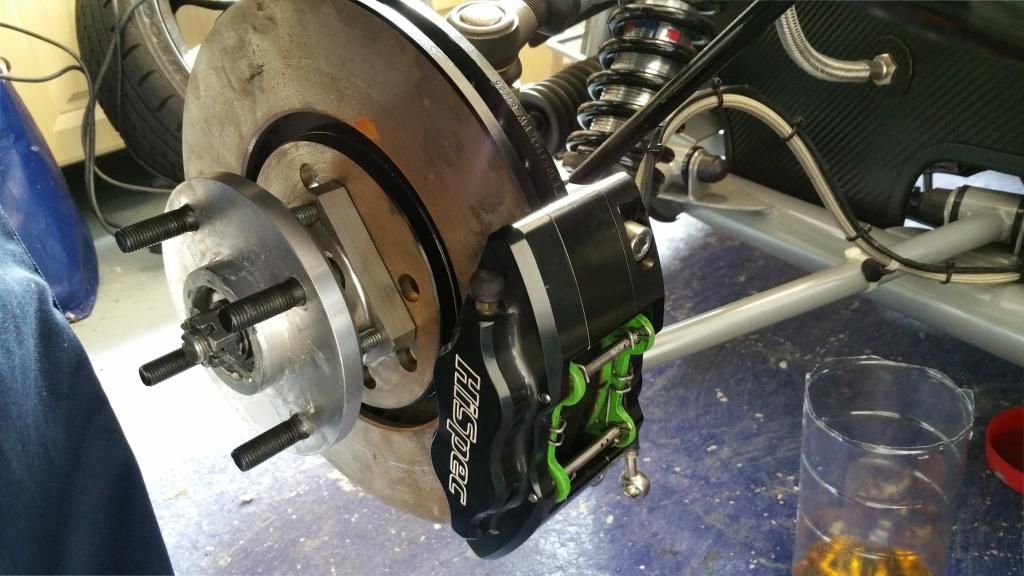
|
|
moz
Junior

Posts: 49
|
Post by moz on Jun 30, 2018 15:44:40 GMT
Hi its not the castellated end that comes loose its the bolt through the back which is the problem ive just come back from a 10 mile run and the nsf wheel was grinding i jacked it up and there was about an inch of movement top and bottom of the wheel very disconcerting and i have had the hub bolts modified to prevent this by welding a threaded bar to the bolt head and attaching that through the wing stay bracket and securing with a lock nut. But the bolt still came loose. I know this is an old topic but has anyone found a viable solution thanks andrew
|
|
|
Post by Stiggy on Jun 30, 2018 22:47:51 GMT
I assume you refer to the stub axle rotating, in which case lease see my previous post regarding a key way or grub screw.
|
|
|
Post by kiwicanfly on Jul 1, 2018 0:58:53 GMT
i have had the hub bolts modified to prevent this by welding a threaded bar to the bolt head and attaching that through the wing stay bracket and securing with a lock nut. Firstly throw those modified bolts out, welding anything to a bolt head will have a highly negative effect on the strength of bolt, this gets worse the higher the bolt rating. I know this is an old topic but has anyone found a viable solution thanks andrew Can you post a picture of the way you have assembled this it might answer some questions, I have had my car on the road over two years, driven it hard, spun off a track, hit a bank hard but never had that bolt come loose. In absence of a picture - How thick is the washer under the head of the bolt? In the case of an assembly from the standard RD kit It needs to be thick enough not to distort when you tighten the bolt. In the case of an assembly where the bolt passes through the wing stay have you placed an adequate spacer in the gap between the stay plate and upright? Whichever of the two options above are selected it is critical to get the support to allow correct tightening. Next is the bolt tightened to the correct torque? As Stuart points out an m12 g12.9 bolt requires 125Nm of torque, you can only get that with a sufficiently long lever. A standard spanner or (even worse) allen key just won't get you there. Also for one of the most critical bolts on the car the tightness needs to be measured, only a torque wrench can do that. If you haven't got one borrow one of get it done for a couple of beers. Is there enough thread on the bolt? You want at least 1.5 times the thread diameter inside the axle so 18mm of engagement for an m12 bolt. With that amount of engagement the axle will stand the torque level, look how much of thread you have on a nut. Have you put a mechanical locking device under the bolt head? A locking washer of some description. I personally prefer Nordlock washers but there are others such as your basic spring washer that have been used for years. I don't RELY on locking compounds and personally don't think you should basically because they are often relied on in place of basic good practice however using them in ADDITION to good practice is fine. Because this has happened before there may have been damage to the bore of the upright, the bore may now be slightly oval, if this is the case you will be able to notice it if you put the axle in the bore without the bolt, push it home and see if there is any rocking whatsoever. In theory there should be none but if you do feel some don't panic, compare the rock to the driver side as it might just be coming from standard clearances. However if badly oval you will need to replace it, RD may sell you that part alone. So in summary you are tightening the bolt to the correct torque with a locking device under bolt head and pullIng down onto an adequate supporting surface. In my opinion this is the only viable, or required, solution.
|
|
moz
Junior

Posts: 49
|
Post by moz on Jul 1, 2018 10:31:30 GMT
Thanks for the very comprehensive reply, this modification was done by a kit car specialist garage in Scotland and they said the original bolts were not long enough and replaced them for longer ones with a thick washer and it was their solution to weld the extension on im thinking there is probily wear between the stub and the hub. This will need to be replaced i suppose but im also thinking of changing the front brakes back to standard as they seem far too large for the size of the car and the effort required to get them to work is unnecessarily hard. so quite a bit of expense looming thanks Andrew ps will try to upload a picture
|
|
|
Post by kiwicanfly on Jul 2, 2018 10:24:14 GMT
I've never hear anyone complain that front brakes are too large, it's a first. If they are too hard to push then change the master cylinder size. Regarding the "specialist" who welded a stud to your bolt have a look at this www.physicsforums.com/threads/welding-on-fasteners.363914/By the way have you told them that they have come loose again?
|
|