|
Post by mawdo81 on Mar 1, 2015 8:16:49 GMT
BonnetAnd, all done. Focus gas strut is too strong, real shame, I'll see if I can find one that needs less welly to close. Try b&q or equivalent -you can get adjustable ones for kitchen doors that pivot on the horizontal.
|
|
|
Post by casesensitive on Mar 1, 2015 13:30:35 GMT
Yeah, I put gas strut into ebay search, and saw the kitchen ones, so I'll pop out to the big B&Q in liffey valley during the week. Brucey-bonus, they're cheap! Also, one was helpful enough to provide a table from which I could work out the load maths. Load rating (Nm) = distance from fulcrum (M) x weight/load.
Which is Archimedes' law of the lever, duh.
I need to figure out how hard I want to have to push the bonnet down; I know I can't close the focus strut with one hand, so pushing down on it might cause the 8 M4 rivnuts to pop out of the chassis at the other end, or worse, the 8 in the bonnet to crack the GRP. I'd like the bonnet to gently open when I pop the catch. Like on the ma's Rover 75, and possibly lots of other cars.
With RTR gone to the wall, the chances of getting a new bonnet are slim, so though it took me the whole day to do one small bit, I'm being super careful not to mess it up!
|
|
|
Post by kiwicanfly on Mar 2, 2015 5:23:16 GMT
It is actually Nm not nM  The capital N is used because it is named after a person, in this case the great man Newton himself. Lower case m from distance, in this case metre. However this is most important to remember because you have to work in Newtons which is the weight in kg x 9.81 or gravity. So simply using your bonnet weight at around 5kg would give you a result out by a factor of about 10. You need also to get your centre of gravity for the distance, I did the same exercise and found this by means of a great mathematical formula taking into account the bonnet taper, the core thickness and resin density allowing of course for the additional weight of the aerocatch and screws minus the grp you cut out...........  Or you could stick it on a narrow piece of wood and shuffle it till it balances 
|
|
|
Post by mawdo81 on Mar 2, 2015 12:56:59 GMT
If you want to complicate things the load will change as the angle of the bonnet about the hinge changes ;-) To take it to extremes, when the CoG of the bonnet is directly above the hinge (and you're not accelerating or braking ;-) the full load is through the hinge and nothing on the strut...
|
|
|
Post by casesensitive on Mar 2, 2015 13:16:30 GMT
So simply using your bonnet weight at around 5kg would give you a result out by a factor of about 10. ah yes, but I did say Weight, not Mass ;-> My plan had been to temporarily fit the strut, stick a weighing scales on the top of the bonnet, and push down with exactly enough force to close it, multiplying by 10. Of course, that would only tell me force I'd need to close the one I have. Then go out and buy one 1/3rd as powerful/resistant from ebay/kitchen shop. Things like lift length would be an issue, the load on the corner I fit it to, as would the holes I'd just made in my irreplaceable bonnet :-O I do still have the gammy Ford bonnet prop..
|
|
|
Post by casesensitive on Mar 2, 2015 13:47:49 GMT
Primitive though it might be, I could hold the scales under the bonnet at approximately 30-40cm from the hinge, lift up the bonnet and watch the display. Multiply the biggest number I saw by 9.81, then multiply by 1.5 to be certain, and use a gas strut of that lifting power, no?
|
|
|
Post by mawdo81 on Mar 2, 2015 16:12:16 GMT
Get them from a local shop, not online. Make your best guess, the above seems ok. Temp fit it, even with a helper to hold in place and try it out. Not right, take it back and change it for one more or less powerful?
|
|
|
Post by kiwicanfly on Mar 2, 2015 18:39:40 GMT
It really depends on what you are trying to achieve.
If the intention is merely to hold the bonnet open then you will only need a weak one as the load vertical is minimal at most when open.
If you are looking to have the bonnet gracefully and gently rise after flicking the catch then it is more complex.
Personally I would go for simply holding it open as that is the primary function and bonnet "tricks" loose their novelty really quickly. Also, and more importantly, you will need quite a strong unit to lift the bonnet from the closed position and all that force is going to be pushing sideways on the fixings which are only anchored in a "bit of grp", I can see it working loose and damaging the bonnet over time.
|
|
|
Post by pocketrocket on Mar 3, 2015 1:14:40 GMT
If & when someone works it all out, can you let me know.
I'm not to bad working with springs, shocks, weight distribution etc etc, but I reckon you've all confused the cr@p out of me with this. But I think it would be a neat feature to have
|
|
|
Post by casesensitive on Mar 22, 2015 23:33:30 GMT
Update on the gas strut thing. Not sure my redneck-science-project method of working out the strength of strut required really worked. On the surface of it; it started out soundly. I calibrated my instrument, and I took 5 measurements, eliminating the highest and lowest, and averaged the other 3. It went a little downhill after that. Might need to actually use some of the maths I took in college, but I'm not sure differential calculus helps here. Anyway, my thinking was that I'd stick a scales under roughly the point at which I'd mount a gas strut, and lift the bonnet from there, taking readings just as the bonnet is starting to lift. Average was about 6.9kg, which would give me 68Nm. First problem is that the scales were tall, so the first bit of the lift isn't where I took the reading.  Then I measured the force of the focus one, which honestly it's difficult to compress with your hands, I generally lean on it. So I did this, on the same scales, pushed steadily harder until the strut compressed and took the usual measurements. Average was 19.3kg, or a touch under 190Nm. Which all seemed about right.  Then I looked up the struts for other cars' boots on ebay, and it looks like I must be fundamentally wrong in my method, because they're mostly in the 700-1000 Nm range. Kitchen door ones tend to be very short and 60-120. I had a look in 2 furniture shops, 2 homewares shops and B&Q, not a sausage. I'll phone ikea and see what they've got, but I'm not hopeful, which is annoying because anything I get posted from the UK will cost a load more in postage than the thing is worth.
|
|
|
Post by casesensitive on Mar 22, 2015 23:38:21 GMT
Grubby jobHonestly, hardly worth a post, other than for a useful enough tip I found. While marking the holes for my bonnet hinge I used crappy old masking tape, which didn't come up as masking tape should, and instead left this goddawful mess.  Been annoying me for a while. Googled how to get up old masking tape, and good old WD40 came up. I've been using it mostly for cleaning things since I learned of silicone spray and copper grease on here as being the actual thing you need for most of the things I'd used WD40 for in the past. 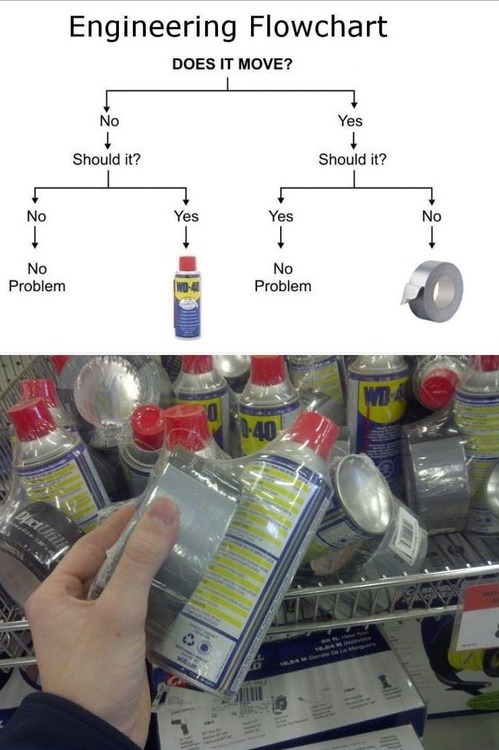 Any excuse to get that in. Anyway, plastic scraper thing plus WD40 and it came off handy enough, got it all off in about 10 mins. 
|
|
|
Post by casesensitive on Mar 23, 2015 0:06:56 GMT
Weight gainI doubled the weight of my Rocket this afternoon :-) Picture heavy, sorry. I found that my engine and gearbox combination (ST170 w Getrag) is a very snug fit, and will only drop in in a very specific sequence. Might also work some other way, but this is the only way I could get it done. Swaddled it like a newborn, but crucially, omitted to protect the lower wishbones and the two horizontal cross members that separate the engine bay and the passenger cell. I put this right after scratching all 4 a bit. Take off both mounts if they're attached. I tried with them on, just didn't fit.  Go in diagonally, with the gearbox mount about 15-20cm further forward than the other.  Then I dropped the engine 1cm at a time, checking clearances all around in between, kicking and cursing as I went. A helper would have been useful, but my Gran's 90 and her eyesight isn't great. I dropped it a good bit below where the gearbox side lines up. I don't have a load leveller either, so this all had to be set with the angle of the strap.  Couple of things to watch out for, wishbones, exhaust manifold (had to give this several sturdy boots to 'realign' the engine. And this little beggar, dead easy to put the whole weight of the engine on this and snap it right off, catches on the horizontal cross-member at the back.  Then I lined up the gearbox side, raised it up 3cm over where it needs to end up, attached mount, and lowered it back down. A lot of kicking, levering etc was needed to correct the weird angle of attack I opted for. 
|
|
|
Post by casesensitive on Mar 23, 2015 0:13:47 GMT
Engine mount side I struggled most with this one for sure. Starting with mount off, I dropped this side to about here, so I could get the mount loosely over the bolts. Angle all wrong so far.  Fiddle and shake, add mount, without tightening the nuts at all. Bang mount into hole, just a bit, whack until approximating over the hole. Lower 2cm, enough to get the M12 nut on. Then lower 3 more, tighten nut up before lowering it so far the bolt touches the 'box' of the mount. WTF? Finally, I tightened up the nuts on the mount, which pulled it into place. 
|
|
|
Post by casesensitive on Mar 23, 2015 0:20:24 GMT
Hmmm, lots of issues, exhaust manifold protruded very badly into the cabin, gearbox side sitting right on nearside wishbone, Definitely no room for a supporting brace here.   It's all in the torque link, it pulls the engine quite a bit back when properly attached. Did this up with the original bolt and a second hand nut, both of which need new ones, so no pictures of them. I found that opening up the bracket the horizontal part of the mount (the 'front' bit) attaches to made this go a lot easier. Start with the 'back' bit, I pushed the M10 bolt up from underneath so any extra threaded bits were pointing into the engine bay and not trying take the tops off speed bumps. But everything just about squeezes in with it tightened.  Aaand all done! Dead handy to have everything where it'll be finally, so I can measure up cables and pipes.  
|
|
|
Post by BobN on Mar 23, 2015 7:44:25 GMT
Looks great and impressive that you did it on your own. It took 3 of us to put my engine in.
Bob
|
|